Historical
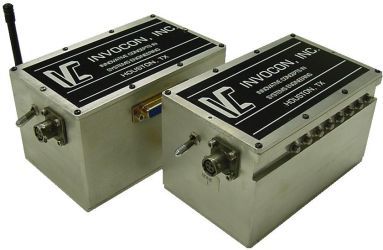
NASA Dryden Flight Research Center awarded Invocon a contract to gather and process data from airframes that would be used to predict failures in critical airframe structures. The sensor network gathered and transported sensor data for complex, real-time, mathematical transformations that must differentiate normal airframe behavior from the behavior of the structure containing a flaw.
Energy from normal flight dynamics, slipstream, turbulence, engine vibration, and control inputs were used as the “impulse” input to the airframe. The airframe response to these inputs was then analyzed for responses that indicated changes in the airframe structure.
At the end of the Phase I work on this project, a system was built and installed in a general aviation aircraft (a Cessna 310 Twin Engine). This system was installed on the aircraft for over two years in all types of flight conditions. Data from the starboard wing of the aircraft could be monitored in real time in the passenger compartment of the aircraft without wiring to the wing. This prototype system was demonstrated to Dryden personnel by flying the aircraft into Edwards and providing a flight demonstration to the engineers involved with the project. This system has provided valuable real-world data for system development. Test flights resulted in carefully flown maneuvers so that the resulting data was specifically representative of a flight condition. The initial system was directed toward low frequency data.
Installation and operation of the Phase I system also demonstrated the interference-free characteristics of spread spectrum techniques. The spreading sequences used on the Phase I hardware were very simple. They provided interference-free operation with all the systems on the aircraft, which included navigation and communications from 200 KHz to Radar and GPS. No interference with any system was observed from the 902 to 928 MHz spread spectrum transceivers. The system used a modular architecture for the hardware, which allowed the ability to interchange the sensor components for each application. Phase I produced a hardware suite that interfaced to a laptop PC for display of the flight test data. As different flight situations (taxi, takeoff, bank, and landing) occurred, the PC displayed the inputs to the sensor evidencing each situation.
Phase II involved fine-tuning the system to accept various sensor inputs, but focused on vibration data.Phase II also led to the final development of the INVision Algorithm, a three-step neural network process:
- Time or Frequency Domain Processing,
- Feature Reduction, and
- Neural Network Classification.