Historical
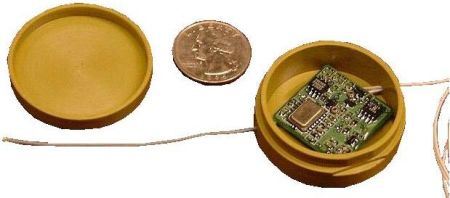
This project concentrated on the miniaturization of wireless instrumentation system technology. The development effort included the conceptual design, fabrication, and demonstration of a battery-powered, miniature wireless temperature sensor.
The prototype device provided reliable data over the entire industrial temperature range (-40°C to -85°C) while consuming only tens of microamps in the active data acquisition mode and several milliamps in the transmit data mode. The size of the unit was equivalent to stack of five quarters. The project specifically addressed the need to decrease the installation costs and spatial requirements of instrumentation.
The development focused on implementing Invocon’s existing wireless network communication system with a MEMS sensor (Micro-Electro-Mechanical Systems) and thus furthering the capabilities of both technologies. Invocon applied the MicroWIS technology to the NASA Johnson Space Center HEDS (Human Exploration and Development of Space) program. The MicroWIS system flew as a Development Test Object (DTO) on Shuttle Mission STS-101 in November 2000, and successfully acquired temperature data from several key locations in and around the Shuttle Crew Compartment and avionics equipment.
The system consisted of the wireless sensor (< 1in3), a PC interface unit, and a graphical user interface. The system development was funded by NASA Johnson Space Center (JSC) to help reduce the integration costs associated with wired sensors. Typically, the cost of cable/sensor installation and drawing changes far outweighs the cost of the electronic equipment flown. The system has been determined to be small enough to survive launch loads when mounted with epoxy or Velcro, thereby drastically reducing integration costs.
The system has flown and operated successfully on STS-92, STS-96, STS-97, STS-100, STS-101, STS-104, STS-106, and STS-108.
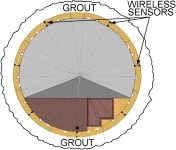
The MicroWIS system is being used to monitor external grout pressure during construction of two tunnels in the Netherlands. Grout pressure determines the amount of grout that is deposited on the outside of the tunnel and is critical to the water-seal and durability of the tunnel. Click here for more information about this MicroWIS application.
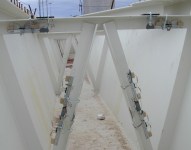
In 2002 the MicroWIS system was used to monitor the stresses on a bridge during the construction and testing phases because there were concerns that significant fatigue was induced during construction.
Click here for more information about this MicroWIS application.
In 2002 the MicroWIS system was updated and replaced by the MicroWIS-XG (Next Generation) System. Click here for more information about MicroWIS-XG.